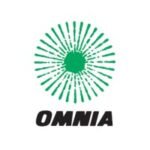
Website Omnia Holdings
Job Description:
A self-driven, hands-on and independent Process Engineer to support the production plants. To optimise process parameters and come up with improvements to optimise production from an efficiency point of view. Design, build and commission projects and ensure all operating procedures are written and implemented. All activities, roles and responsibilities are aligned to the world class (manufacturing) philosophy, principles and practices.
Job Responsibilities:
To ensure process safety adherence: • Prevent occupational and process safety incidents by implementing integral safe design principles. • Conducting risk assessments for tasks and process deviations. • Facilitating Design Reviews, risk assessments and Hazop Studies to minimise risks of new projects. • Find root causes and mitigating actions to prevent/eliminate safety incidents. Drive high performance targets with the team: • Process development and process design. • Driving focused and continuous improvement. • Review expense report and correct deviations. • Correct performance deviations. • Communicate progress to performance indicators to all levels. • Identify process deviations, their root causes and take corrective action. • Ensure reliability of processes. • Managing costs according to budget. • Providing technical support to production facility. • Mass and Energy balancing. • Developing process flowsheets, schematics, process and instrumentation diagrams and control flowsheets. • Continuous Improvement of processes. • Equipment sizing, procurement and Commissioning. Effective project and team management: • Frequent engagement with Production and other relevant stakeholders. • Resource & Project Management. • Factoring safety risk, maintenance costs, capital expense into plans. • Procuring equipment, instrumentation, piping and valves. • Testing control loops. • Lead in Pre, cold & hot Commissioning. • Establishing Basis of Design, conducting feasibility studies and responsible for BEP and managing EPC for projects. To ensure quality adherence: • Monitor and take corrective action on quality deviations.
Job Requirements:
Knowledge • Familiar / Competent in Microsoft Office • Competent CRS Payroll Solutions Core Behavioural Competencies • Decision making • Teamwork • Work standards • Reliability • Motivation of self and others • Adaptability • Problem-solving • Integrity and trust • Communication skills • Planning and organization • Stress tolerance • Initiative • Building relationships Functional / Technical Competency • Coaching and Mentoring • Facilitation / Meetings • Charing Disciplinary Enquiry • Project Management • Effective Change Management • Brand Knowledge
Qualification & Experience:
- 3 – 5 years Experience in a Chemicals Industry
- Fertilizer Manufacturing experience will be highly advantegeous.
- Strictly Minimum B.Sc/BEng Chemical Engineering
Job Details:
Company: Omnia Holdings
Vacancy Type: Full Time
Job Location: Sasolburg, Free State, SA
Application Deadline: N/A
Vacancieshut.com